1.산화(Oxidation)란? : 산화란 산소와의 결합, 수소의 떨어져 나감, 전자 수가 줄어듦을 의미하며, 환원은 산소와의 분리, 전자 수가 늘어남을 의미한다.
2. 반도체에서 산화(Oxidation)란? : 일반적으로 실리콘 표면에 이산화실리콘(SiO2)를 형성하는 것 = 산화막을 형성하는 것.
3. 산화막의 용도 :
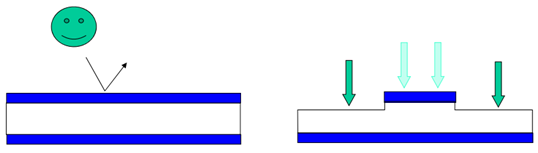
4. 산화막의 방법과 종류:

5. 산화 메커니즘
- 초기 상태에 산소가 실리콘과 직접 결합한다.
- 시간이 흘러 산소가스는 산화막을 뚫고 들어가 실리콘층과 반응해야한다.
- 이로 인해 산화막 성장속도는 지속적으로 감소한다.
6. 산화에 영향을 미치는 요인
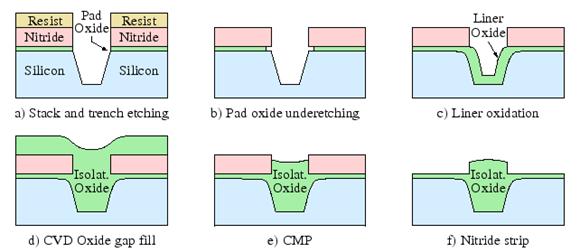
1. 도핑 – 확산(Diffusion) 공정 :
- 농도차를 적절히 설정해줘야한다
- 온도에 따라 확산 속도가 달라진다.
-
불순물이 안정적으로 퍼지기 위한 시간이 필요하다
1) 전부착 단계(Pre-Deposition)
- 실리콘 웨이퍼 안으로 불순물 주입
- 800 ℃ ~ 1100 ℃
2) 드라이브인 단계(Drive-In)
- 열처리를 가해 불순물을 활성화시킴
- 주입 깊이 및 농도 조절
- 1000 ℃ ~ 1200 ℃
1) Constant Source Diffusion(고정 소스 확산)
- 상대적 긴 Pre-dep. + 짧은 Drive-in
- pre-dep를 오래 하면 상보에러함수 형태를 띰
-표면 농도가 일정한 상태로 유지되게 함
- 외부에서 dopant를 지속적으로 공급
- 상보에러함수 형태의 확산식
2) Limited Source Diffusion(제한 농도 조건)
- 짧은Pre-dep . + 상대적으로 긴 Drive-in
- drive-in을 오래하면 가우시안 분포 형태를 띰
- 전체 도핑된 dopant 양이 일정함.
- 외부 dopant의 공급 없음
- 가우시안 분포의 확산식
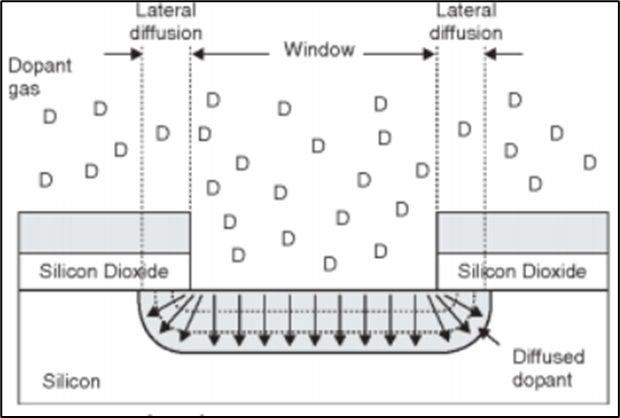
- 확산공정의 큰 단점중 하나로, 화학반응이다 보니 방향을 조절하기 어려워 불필요한 방향으로도 측면 확산이 이뤄져서 불필요한 부분에도 불순물이 주입되는 경우가 있다.
1. 도핑 – 이온 주입(Ion Implantation) 공정
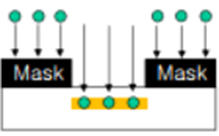
1) 이온 주입(Ion Implantation)
- 가속시킨 이온을 원하는 위치에 강제로 주입함
- 마스킹 레이어로 질화막, 산화막, PR을 사용함
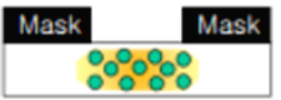
2) 드라이브인 단계(Drive-In)
- 주입된 이온을 활성화 시킴
- 두께 및 농도 제어
- 1000 ℃ ~ 1200 ℃
- RTA(Rapid Thermal annealing)라고도 불리며, 고온이고 아주 빠르게 진행함
- 낮은 에너지, 낮은 농도, 빠른 속도로 스캔할때 얕게 도핑된다.
- 고에너지, 높은 농도, 느린 스캔속도로 이온을 주입할 때 깊게 도핑된다.
- 그림자 효과 : 이온 주입 입사각이 수직이 아닌 경우 사각지대가 생김
- 채널링 효과 : 결정구조 때문에 깊은 깊이의 이온 주입이 발생함.
'반도체 8대공정' 카테고리의 다른 글
[반도체 8대공정] 5. 박막 증착 공정 (0) | 2021.11.29 |
---|---|
[반도체8대공정] 3. Photo공정 (0) | 2021.11.29 |
[반도체 8대공정] 4. 식각공정 (장비구성, 동작원리) (1) | 2021.11.26 |
[반도체 8대공정]4. 식각공정(ICP, CCP, 공정 불량 이슈와 해결법) (0) | 2021.11.25 |
[반도체 8대공정] 4. 식각공정(공정) (1) | 2021.11.25 |